The development of smart materials that could deform and contract
in response to signals or the environment led to new ways in which
vehicles could move about in their environment. One particularly
successful adaptation of these new materials was in marine vehicles,
which could through the use of these ‘artificial muscles’ (also
known as electro-active polymers) mimic the motions of aquatic animals.
This bio-mimetic propulsion started a new era in marine technology,
because the movements they were copying were the result of millions of
years of evolution these types of drive system were greatly more
efficient, and were far less noisy than other methods. The military had
particular interest in these technological applications, as marine craft
could be active yet were all but silent to any hydrophone. This form of
propulsion also greatly expanded the speed ranges capable underwater,
and even small vehicles could travel at exceptionally fast speeds.
Though the military had a great use for these propulsion systems,
scientists were also using them to investigate the depths, the
efficiency of these craft meant that power consumption was small, and
the smooth motions and minimal disturbance of the water led to better
instrument recordings.
The use of smart materials has
undergone further evolution inside Federation history, and although
marine transport and warfare are pretty much obsolete the need to
explore the sea has not, so these forms of propulsion live on in new
vehicles. The early problems with these technologies were that the
volume of ‘mobile hull’ was quite large, not just the elastic
surface but also the banks of artificial muscle underneath. In science
vessels this was not a major problem as most of the craft were
originally unmanned, and so it was acceptable for the craft to
predominantly be made from the smart materials. For manned ships a
compromise had to be made, the crew require pressurised (in most cases)
working environment, which is a pressurised metal container, as this was
rigid the propulsive apparatus had to be built on the side of this. The
best compromise, which is still use today is the use of propulsive vanes
that run the length of the vessel. When in operation these vanes produce
rhythmical waves which forces the vehicle through the water, the motions
are themselves another copy from existing marine life. The vane
technique requires only a small volume of flexible material, but still
enough to achieve moderate accelerations, the other advantage to these
parallel vanes is that with computer control and inertial sensing the
craft can be made to hover in the marine environment or perform more
nimble manoeuvring.
A diagram of a linear
array of vane elements
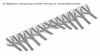
The predominant changes to the
materials used for propulsion are only really apparent at the extremes
of the technology. For general applications, such as for small pleasure
craft, or scientific vehicles, the vane design is pretty much unchanged,
the vane material is composed from mobile layers of flexible polymer,
which contract when an alternating current is applied. These stacks of
sheets form crude ‘muscles’ which are grouped in opposing pairs,
with one of their ends attached to hull, the other to a flexible beam
that juts from it. The movements from the ‘muscles’ can point the
beam in different orientations, and this set up provides the basic
elements for the propulsive vane, which is simply a line of such units.
Other the whole assembly a flexible and robust polymer coat not only
shields the individual parts, but also smooths out the shape creating an
almost perfect hydrodynamic surface. Though this particular design may
seem complicated, but in reality for a small craft there are perhaps
only 10 or 20 elements in each vane, each with perhaps four muscle
groups each, even a simple computer can handle this number of elements
with ease, and a more complex one can optimise the use of these elements
for any kind of manoeuvre. The disadvantage to this design is that there
is a lifetime to the individual components, the muscle sets slowly
degrade, and the beams can fail from fatigue, and although individual
failures are not important for the entire propulsion system, they do
need to be replaced. Maintenance for these vehicles requires the removal
of the outer membrane, which would probably be replaced at the same time
(more from biological adhesions than damage), which would then reveal
the complex banks of muscles arranged around the driving beams. These
units are simply swapped out with new parts. Although maintenance is
straightforward it is often messy as the vane is often pumped with
lubricant, the materials now used in the Federation have relatively
broad lifetimes, and still operate under easy conditions (low voltage,
liquid media and low strain), though degradation especially from
continuous use.
Though this design is
commonplace other designs are widely used, often variants on the same
theme, however there exists a completely different way of forming the
hydrodynamic surface. Rather than making use of flexible polymers, the
vanes and fins could be constructed from micromachines, which can
continuously reassemble into new designs as the need requires. Movement
of the surfaces is simply achieved by scaling the motions of the
individual units in the whole structure. This technique is extremely
advanced, and such ‘active hulls’ are only really required for
extremely sophisticated applications. These methods also require much
more power, and much more computer processing, though the later can be
an integral part of the micro machine components. This kind of
technology is allied to nanite nanotechnology though in this the
component parts are only capable of movement and repositioning, and do
not possess any processing capability, as such this kind of technology
does not pose the risks with other nanotechnologies.
|