All
driver cores contain a special type of material, a substance that can
convert high temperatures and high energy radiation into a spatial
curvature, but by converting this available energy into work, it reduces
the temperature of the local environment, this self cooling property of
driver coil material (DCM) is essential to its design. In addition to
automatic lowering of its temperature this material if it heated above a
critical limit (depending on material type between 1980’K and
3000’K) it loses its space bending properties, very much like an
overheated magnet, however upon cooling the material spontaneously
regains its properties, though it requires a ‘recuperating’ period
before it does so.
The
structure of today’s driver coils is optimized to allow for sufficient
heat to be supplied to all parts, which increases the power density of
the driver core, and also to prevent high temperature regions which
degrade its performance.
The
principle structure of the core is based around a superconducting
scaffold, whose main principle is to distribute energy throughout the
core component. The wires of the this superconducting frame form a dense
mesh, also in which are control and monitoring instrumentation, DCM
material is then ‘grown’ in amongst this mesh forms the finished
core component. A shield of refractory material also forms a shell
around the component, this protects the surface of the component from
the ultra high temperatures of the drive core, as well as providing some
protection from drive plasma. The refractory layer may also contain
superconducting coils which generate magnetic fields which keep charged
ions from ablating the surface. In addition to these basic measures, a
layer of massless neutronium may be added over the refractory layer or
replacing it, with a subsequent reduction in mass, and increase in
driver core power density.
The
advantages of neutronium clad cores also include a longer component life
time, and any ablated material will be in the form of neutrons which
pollute the drive plasma much less than ablated refractory material
ions. However the cost neutronium is to cut out most radiation, which
reduces the amount of energy salvaged from drive plasma. To compensate
for this ‘filigree’ might be added to drive components, these are
basically very fine layers of massless neutronium that act a bit like
heat sinks, but whose purpose is to aid transfer of radiative energy
into the drive plasma.
Refractory
linings are however simpler systems, and are compatible with highly
radiative power plants such as antimatter/matter reactions, their design
also allows for much smaller driver cores, as drive plasma is not
required for most of the energy transfer. The refractory material is
interdigitated with superconductor which cools it, the cooling coming
from the heat consuming processes in the core, this cooling prevents the
refractory material subliming from the radiation, however this layer
does need regular replacement, though onboard systems recycle the
ablated ions of the refractory material. However the refractory material
is rapidly ablated by drive plasma, and for this reason it usually only
used in drives that are completely free of drive plasma (Radiative
Transfer Cores), it does however provide a window for radiation, even
high energy gamma. Driver
Coil Management flow diagram
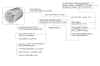
|